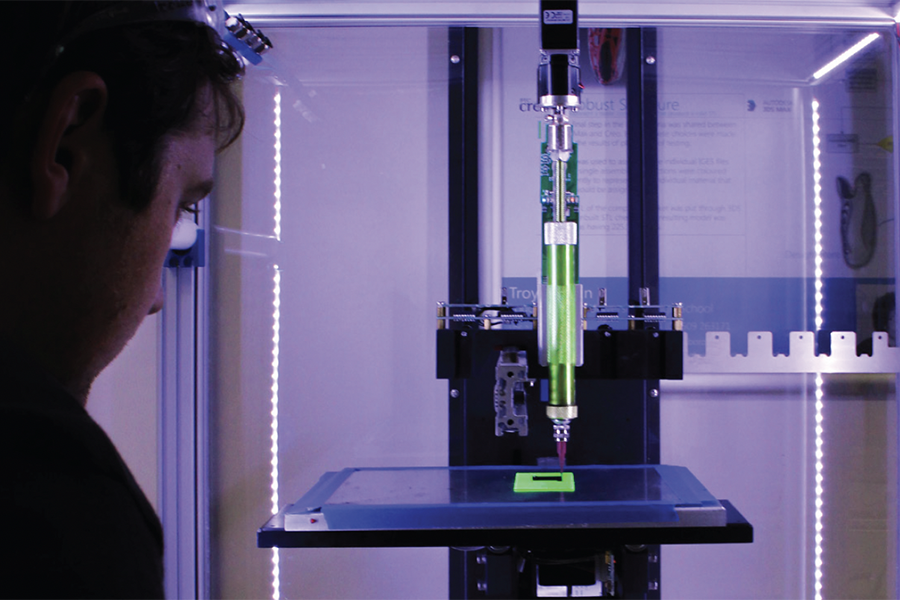
While all of us have heard of 3D printing, only a few experts can claim to fully understand the revolutionary impact that the technology may have on the world’s manufacturing industry. Saudi Arabian entrepreneur and 3D-printing evangelist Faisal Alamer is one of those people.
“3D printing can eliminate the need for inventories and supply chains,” he says. “On-demand manufacturing will reduce the need to manufacture mass-produced parts. These effects are still not obvious to many major manufacturing and supply chain companies. However, there are people who are very aware of what is going to happen, and they are now investing billions of dollars into this technology.”
3D printing, also known as additive manufacturing, is a manufacturing process which puts down layers of materials to create a three-dimensional object. 3D printers take information from digital files about where and how to deposit the materials. Based on this data, the technology brings new objects to life, using a wide variety of different plastics and metals. Within hours, the machines can produce more complex parts than can be made with more traditional manufacturing processes—and at a much lower cost.
“There is a freedom of design and a flexibility that you do not get with traditional manufacturing,” Faisal says. “3D printing makes it much simpler to change the design of a part.”
“3D printing will transform the economics of manufacturing and the global supply chain.”
Faisal Alamer, Founder and CEO, Namthaja
Faisal’s business, Namthaja, has quickly grown into one of the most advanced 3D manufacturers in the Middle East, and counts some of the world’s largest energy and oilfield services companies as clients. Based in Saudi Arabia’s Eastern Province, Namthaja uses 3D printers to manufacture complex components on demand for use in critical operations in extreme conditions. The company also makes increasing volumes of products for clients in the industrial, architectural, and healthcare sectors. Namthaja’s revenues rose fivefold in 2022.
“For several years, we invested in building the market’s awareness of the flexibility and the freedom of design that is possible with 3D printing,” Faisal says. “Now we are reaping the fruits of all our hard work.”
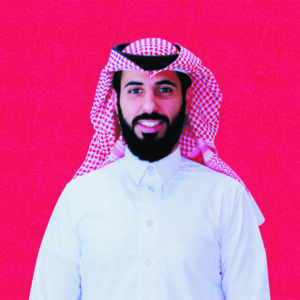
What are some of the main benefits of additive manufacturing?
Currently, the world manufactures mass-produced parts. Companies store, distribute, and sell these parts. 3D printing will lead to a shift towards on-demand manufacturing. Companies will send designs to 3D manufacturers for production and delivery of parts, as and when they need them. Thanks to 3D printing, it is very easy to change designs and make new models without incurring major overhead costs.
What sort of work does Namthaja produce for its clients?
We have clients in three main sectors: industrial, architectural, and healthcare. The first two sectors are currently our main focus. Within the industrial sector, oil and gas is our major priority. We also serve a large number of manufacturing companies. We work with them to produce some of the components that they use to assemble their products. In the oil and gas sector, most of our clients come to us to design and produce spare parts quickly and cost-effectively.
How is business increasing?
We have had an average annual revenue growth of 200 percent since 2018, and last year we doubled that level. Our team now consists of about 30 highly skilled people. We are continuously acquiring new printers. We currently have almost 60 printers in Namthaja, using different technologies, materials, and capabilities. We are always exploring new applications and building our capacities to innovate.
The process of thinking of how we can utilize 3D printing to enhance a specific product or manufacturing process is something that is very exciting for me and my team.
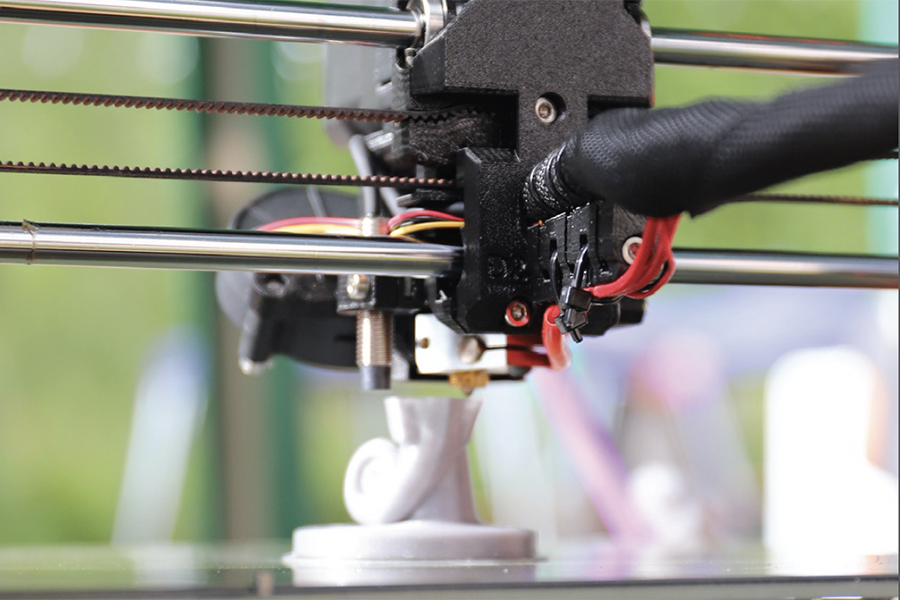
How are you funding this growth?
There is a lot of interest in the potential of our technology, and people believe in our business model. The first round of funding for Namthaja, which took place in November 2021, was highly successful. We have an incredible group of investors, and many of them form part of the growing venture capital community in Saudi Arabia. They gave us massive support during the pandemic. We plan to raise another round of funding in the near future.
What do you think is the future potential of 3D printing and Namthaja?
According to Facts & Factors, the 3D printing market is growing by more than 20 percent per year globally. What I’m seeing through my work is that in Saudi Arabia, we have annual growth rates of 50 to 60 percent. We are experiencing faster growth because our market is not as mature as those in China, Germany, and the U.S. We are going to reach the same level. 3D printing is the best, most flexible option for meeting the needs of local manufacturers for complex parts and components without incurring major overhead costs. The manufacturing sector in Saudi Arabia is growing very fast, and that will drive higher demand for 3D printing.
What innovations are you working on currently?
Our aim is always to convince our clients to replace their previous methods of making parts, such as injection molding, by switching to 3D printing instead. Every part that we make with 3D printing was originally produced with another technology. So we need to be innovative in terms of design, functionality, and cost
Every day, we make changes to the way that we produce parts for our clients. You will not find 3D-printed parts in the market. We invest a huge amount of effort and experience to achieve added value for our clients when we convert them to 3D printing. Every time that we convince a client to convert a part or an application to 3D printing feels like a victory for us.
Making these productive changes in the manufacturing industry is very satisfying and rewarding. It is my greatest source of inspiration
Published as branded content in WIRED magazine.